As long ago as the mid 1990s, we embarked on our journey into designing and manufacturing sustainable textiles for our chosen market segments.
We were a very early adopter of the environmental management system, ISO 14001, back in 1996 when it was largely unheard of. And from a single accreditation at a single site, we now have five manufacturing sites, plus our head office, all operating an environmental management system for “the design, development, manufacture, finishing, marketing, sales and verification of woven and knitted contract and transportation upholstery fabrics”.
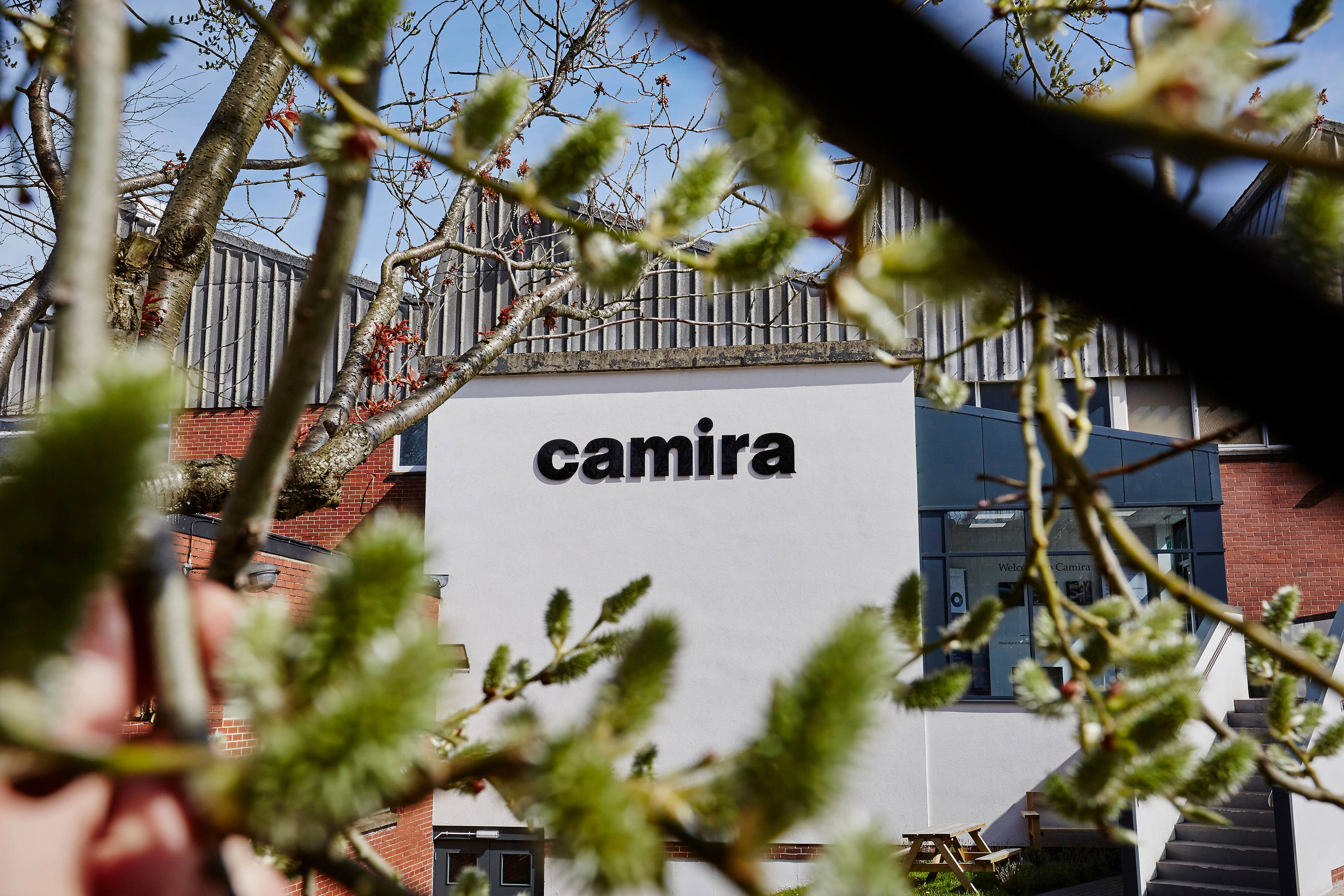
When it comes to sustainable fabrics, we hit the ground running and have never stopped since. Our first dedicated eco fabric was called Ecollection, a natural and renewable collection of wool fabrics colored using the most environmental non-metallic dyestuffs. We pioneered ReSKU, made from recycled woolen army jumpers, and launched our first recycled polyester fabrics over 25 years ago, long before post-consumer PET hit the mainstream. Our SEAQUAL® ocean waste fabrics use post-consumer recycled plastic bottles taken from both land and sea, highlighting the issue of marine plastic pollution and supporting ocean clean-up projects in the Mediterranean, River Nile and Caribbean.
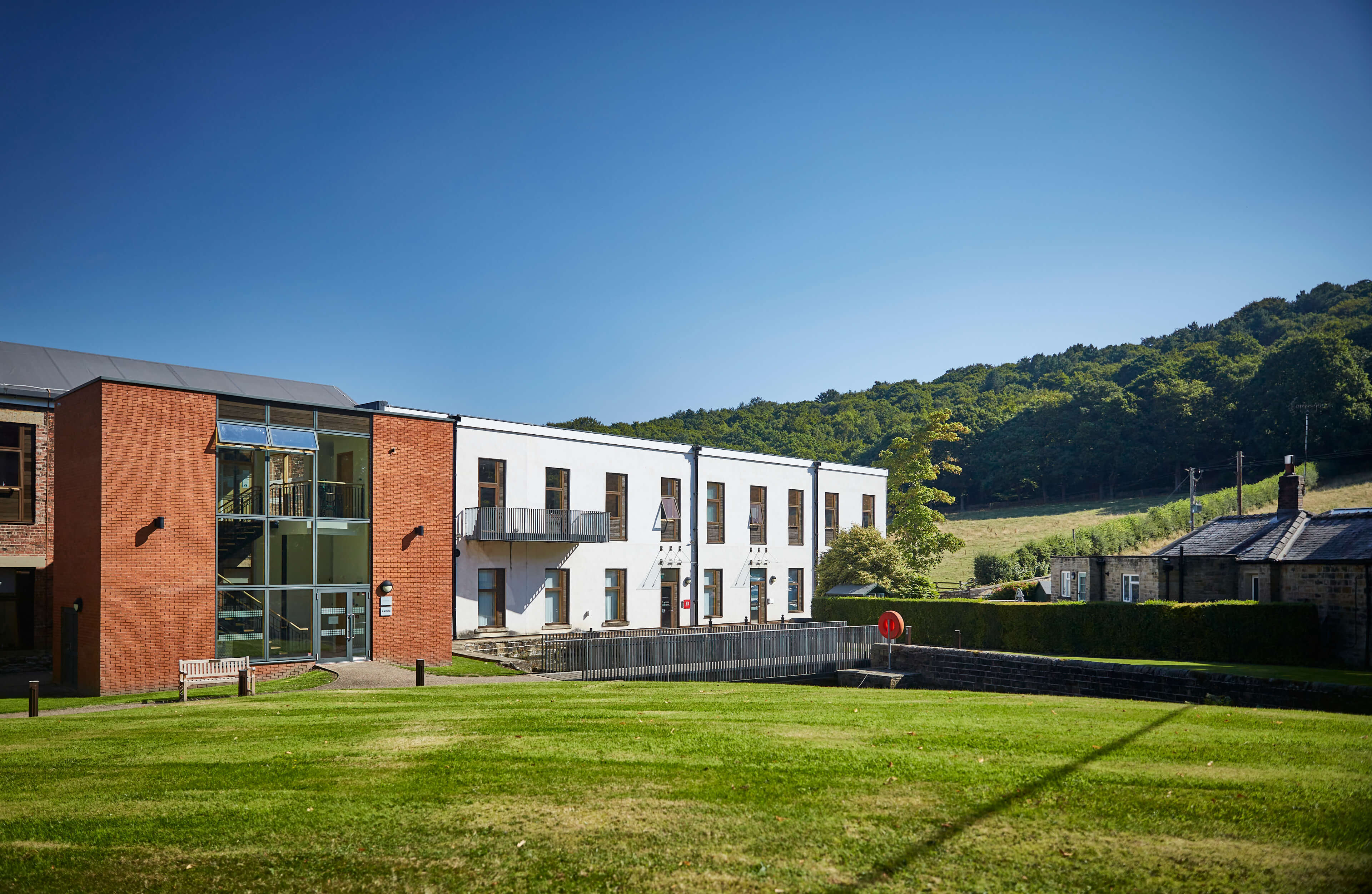
In the mid 2000s we innovated a ground-breaking environmental fabric made from nettles, leading the award winning STING project (Sustainable Technology in Nettle Growing) which fuelled the development of a new category of naturally flame-retardant plant-based fabrics using harvested nettles, hemp and flax. Most recently, we’ve mastered circular, closed loop wool recycling, allowing us to recycle our own waste wool – and the color within it - into new yarn and new fabric to be enjoyed all over again. We have also developed environmental fabric treatments, especially for flammability performance, using non-halogenated FR chemistry.
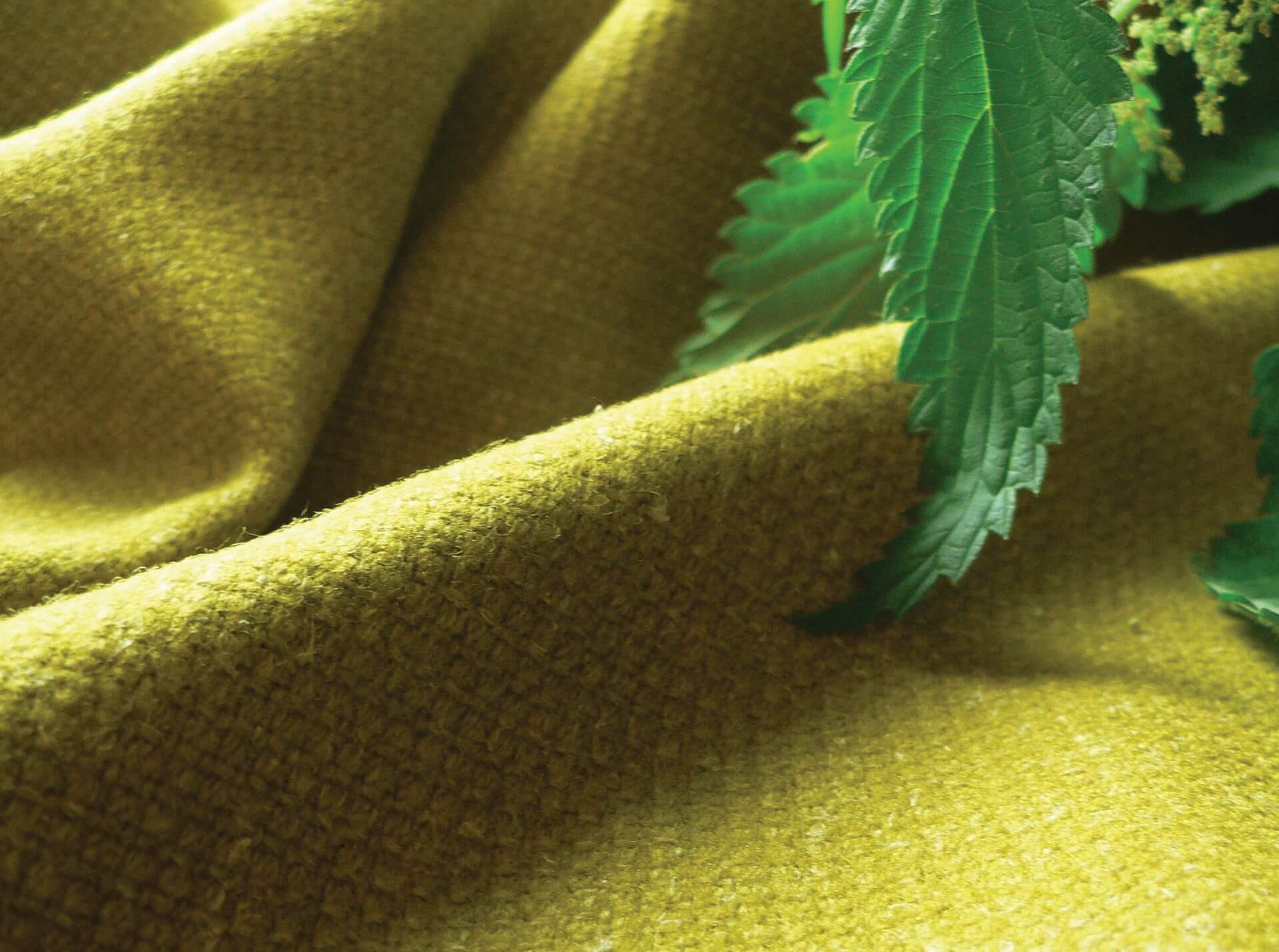
Alongside our environmental product stewardship, we have expanded our vertical manufacturing integration, adding fabric dyeing, printing, technical knitting and specialist upholstery services to our core weaving, yarn spinning and finishing capabilities. This gives more in-house control over key processes, such as water and energy, waste reduction, waste streaming for re-use and recycling, and calculation of our carbon footprint across scopes 1 and 2. We have a proven track record of environmental manufacturing, from borehole water and river abstraction, for use in wool scouring and textile finishing, heat recovery technology, voltage optimization and LED intelligent lighting. Our broader ESG interventions cover demonstrable social actions, both internally and with external stakeholders, and robust corporate governance.